Decades of completing industrial process equipment installations makes Roberts Onsite uniquely qualified to help integrate your new process equipment into your existing facility.
_______________________________
When your car breaks down and you can’t fix it yourself, you probably know who to call. Same goes for the lawn mower, fridge, or washing machine. But when it comes to moving the injection molding machine from one area of your manufacturing facility to another, or installing a new palletizer, the technician’s name isn’t necessarily top of mind.
Finding an experienced company that you can rely on to install or move industrial machinery and heavy equipment used in the manufacturing process is critical to getting your product to market.
Whether you are manufacturing empty beverage cans, lightbulbs, car doors, or designing a wind tunnel, there are various processes involved to create a final product or achieve a particular result. Getting the industrial machinery and equipment required for those processes installed, operational, and maintained is where Roberts Onsite comes in.
Roberts Onsite is one of Ontario's largest multi-trade contractors with more than 85 years of experience. When it comes to process equipment installations, we offer a truly integrated solution to the project. Our comprehensive millwrighting and rigging, electrical, and mechanical departments work cohesively and efficiently together. That is why, 9 times out of 10, we can honestly say, “Yes, we have a technician for that”. Our in-house communications; automation controls; utilities; and maintenance departments round out the complement and help us to provide turn-key solutions for our customers.
Let’s look at some of the various ways Roberts Onsite’s skilled crews handle process equipment installations.
Expert Millwrights to Optimize the Layout and Configuration of Your Industrial Building
Whether it’s a new line that needs to be installed, a system that is being relocated from one facility to another, or an existing process that needs to be reconfigured and expanded, the Roberts Onsite team can help get everything up and running.
Our Millwrighting & Rigging team studies the available drawings to get a better understanding of the full scope of the project. If drawings aren’t available, we’ll work with the owner, construction managers or engineers to help determine what is the best configuration of equipment to address both the customer’s needs and the physical limitations of the facility.
Once the layout is confirmed, our crew will apply datum lines or reference points directly on the floor. These lines enable the team to see the actual location of the various pieces of equipment within the physical space. Looking closely at the physical space will illustrate if there are any existing services that may get in the way of the final placement of the equipment and industrial machinery. It will also give the team an opportunity to make any needed adjustments in places where the floor is not level.
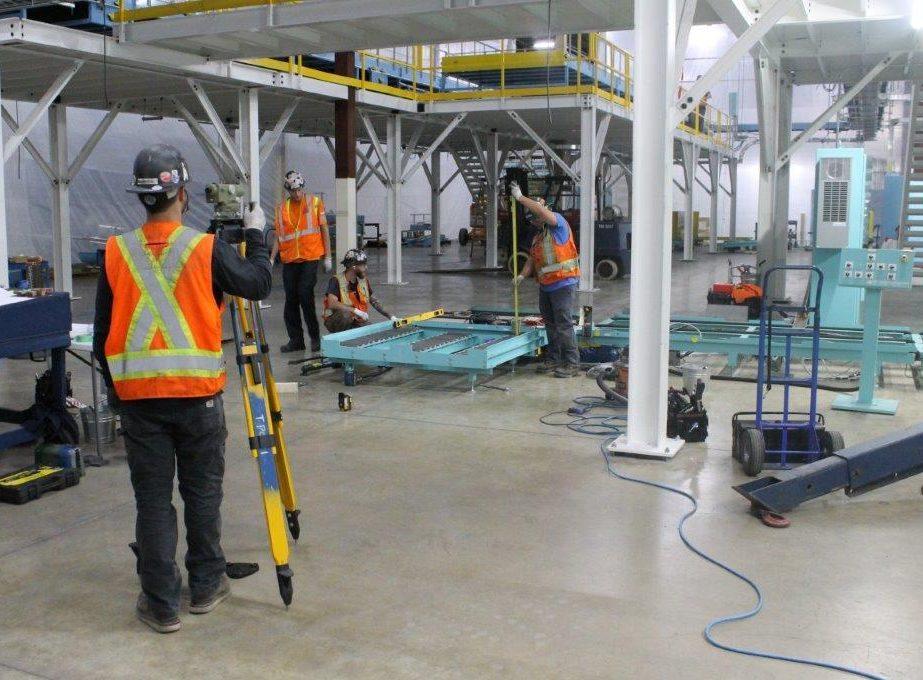
Industrial Millwrights Know this: Placement is Important, and So is Timing
Decades of experience translate into us being able to think several steps ahead to make sure all the pieces of the puzzle can come together.
“I remember we were hired to install a vehicle dynamometer inside a climate-controlled wind tunnel at a research-and-testing facility that was being built,” said Michael Birmingham, Senior Vice President, Roberts Onsite.
Even though Roberts Onsite’s tradespeople were months away from being required on site, one oversized component made the team pause.
“The main roll test component of the system was too large to fit through standard openings. It was also too heavy to cross the floors that were specially insulated. We knew we had to do something immediately. We told the construction manager to halt construction of an exterior wall, leaving us a way to get the machine into the building.”
The team used that make-shift doorway to load the equipment into the partially constructed building. The equipment was tarped and secured inside so that construction could resume. Once the building was completed, the rest of the installation continued with the remaining components being loaded in through conventional means.
Having the experience and ability to assess all aspects of the project proved invaluable in this situation. Taking a full look at not only our scope of the project, but also the work going on around us helps us develop the most efficient and cost-effective strategy for getting everything into the building.
Experienced Millwrights Get the Infrastructure in Place to Support the Installation
The Millwrighting & Rigging team constructs and installs the infrastructure that surrounds the machinery. This can include mezzanines, overhead structural steel, access walkways, platforms, and supports.
To allow us to streamline the installation, our Mechanical and Electrical teams do their own pull-ahead work in advance of equipment being placed. Some of the building services that will support the new equipment are pre-installed: power feeds, network communication cabling; gas, water, and compressed air feeds, and the cable trays that hold all those services.
We will receive and offload the heavy industrial equipment when it arrives at the site. Deliveries will be un-crated and the equipment will be inspected to assess if any damages were incurred during shipping.
Once the site is ready, we will move the equipment inside the facility and systematically set it in position. It is often a bit of a dance to place and level the various pieces of equipment, but after everything is anchored and set, the installation is ready for our electrical and mechanical departments to pick up where they left off.
When the other trades have completed their work, the Millwrighting & Rigging team will circle back to complete a final check of the equipment. They will initiate a thorough start-up of the process. This step is critical to ensuring that the equipment functions the way it is intended. By initiating all the required components and machines in the process, the team is able to make necessary adjustments to machine settings, alignments and tolerances.
If additional elements are to be installed for safe operation of the equipment, such as safety guards, or perimeter fencing, the team will install these as well.
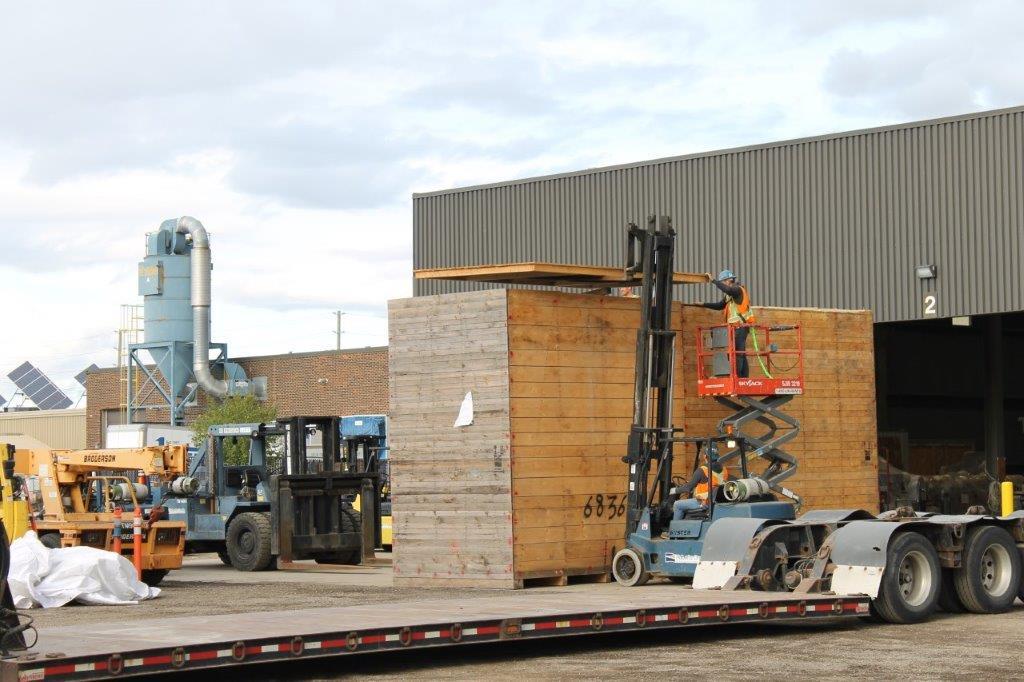
Connecting the Process Lines to In-house Systems
Getting everything into the building is only part of the equation. Depending on the requirements of the processes being installed or upgraded, there are additional service connections that need to be made.
Our Electrical and Mechanical teams use their understanding of the process equipment being installed to calculate the number and size of in-house supply lines required. Power, data, water, hydraulics, vacuums, and pneumatics are just a few of the systems we install and maintain.
Whether it’s a small production line, a large assembly line or a whole plant, power panels will be used to provide dedicated electricity to various components and types of machines involved in the process. To get power from the plant distribution panel to the process panels, our electricians map out the most efficient route for the cable tray and wiring they are installing.
Modular Wiring Systems Provide Plug and Play Convenience
We have extensive experience with modular or “plug and play” panels and systems. These control panels come to site pre-wired with panel mount connectors. Pre-made, and in many cases “off the shelf,” cables connect the control panel to a variety of field devices, stations, and junction boxes through the bulkhead connectors.
The connectors are specifically designed to allow for multi-wire cable to pass into the panels through a single connection which takes only a few seconds to connect. Today, connectors come in all shapes and sizes to suit the design requirements. There are even connectors that can combine power, control, network, and fluid systems making the whole control system truly plug and play. Using this type of architecture significantly reduces the amount of time required to field wire and make final terminations during field installation. When systems are designed and factory tested with this method, wiring mistakes at final site are all but eliminated.
The Roberts Onsite team put this to the test with a recent installation of a new production cell that comprised four assembly stations circling a robot. The equipment was manufactured and tested in the United States and shipped to Ontario.
“The component pieces were manufacturer-tested in the States, then disassembled and crated and shipped to us in Ontario for a robotic process automation cell,” said Wayne Barnard, Vice President. “Our M&R group received the shipment on our customer’s behalf and then assembled and set the robot and jigs in place.”
Our Mechanical team piped in new air and process water feeds required, while our electrical team installed the cable tray to house all the feeds including the power lines. The electricians connected the modular panels with the main distribution and made the interconnections between each of the jigs and the robot.
“The best part of this installation is that from the time the crates arrived in Ontario to when our crews packed up and left site was three days,” Barnard explained. “The modular panels were a key factor in our team being able to hit that compressed schedule. Field wiring the panels and connections would have added weeks onto the project.”
Our Automation Controls group designs, builds, and tests modular wiring system control panels in our QPS-certified panel shop. This in-house capability allows us to have a greater control of the schedule and provide competitive pricing and cost savings to our customers. Panels with bulkhead connectors and multi-conductor cables allow for faster replacement in the cases of cable damages in the future. There is no panel termination required – our crews just quickly swap the broken cable out for a new one.
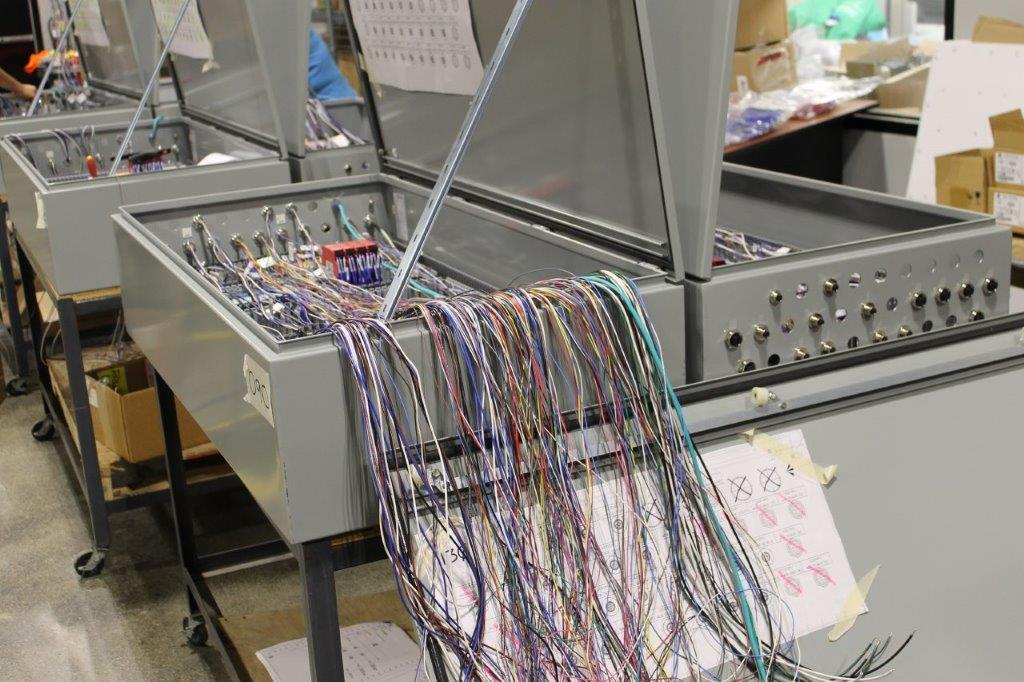
Realize Efficiencies and Cost Savings for Your Projects
Companies are continuously looking for ways to increase efficiencies and output volumes. Our in-house Automation Controls team can refine and perfect the functioning of the system as it is installed. Depending on the requirements, our team can install and program various technologies including sensors and vision systems to monitor the production lines. These types of systems can operate significantly faster than the human eye and are able to scan a conveyor line of products for imperfections and trigger a remedy solution further down the line.
Efficiencies are gained by adjusting the route of the conveyor lines. Conveyors are so much more than a straight shot from point A to point B. They can be designed and routed to incorporate loops that consolidate the product while the process station catches up. These accumulation lines help to prevent bottle necks further down the line and allow for product lines to be changed without causing the entire line to shut down.
Grow Your Team by 300%
Roberts Onsite has three distinct departments: Millwrighting & Rigging; Electrical; and Mechanical. With an existing staff complement that includes millwrights, riggers, iron workers, electricians, pipefitters, steam fitters and so many more, we are equipped to coordinate and schedule the work of all the trades – saving you money, time, and aggravation. A single point of contact at Roberts Onsite makes that possible. We will use our expertise to provide you with an efficient, cost-effective result.
We can work with you to come up with the best solution that fits both your needs and the requirements of the process equipment. Contact us today and add us to your team.
Call 1-800-265-8961 or fill out our online form for a prompt response.